 |
 |
 |
 |
 |
 |
 |
 |
 |
 |
 |
 |
 |
 |
 |
 |
 |
 |
 |
 |
 |
 |
 |
 |
 |
 |
 |
 |
 |
 |
 |
 |
 |
 |
 |
 |
 |
 |
 |
 |
 |
|
|
|
|
|
|
|
|
|
|
|
|
|
|
|
|
|
|
|
|
|
|
|
|
|
|
|
|
|
|
|
|
|
|
|
|
|
|
|
|
|
|
|
|
|
|
|
|
|
|
 |
|
|
|
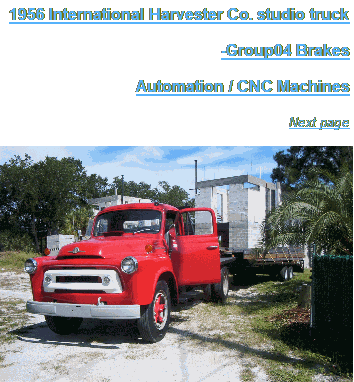 |
|
|
|
|
|
|
|
Chevy 350 for the studio truck
|
|
|
|
|
|
|
|
|
|
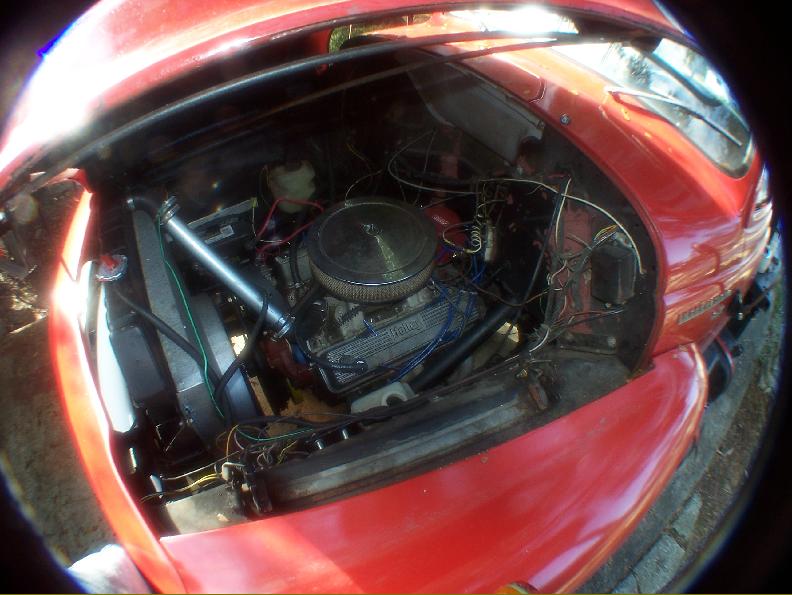 |
|
|
|
|
|
|
|
|
|
|
Chevy 350, hi-torque build Est. torque: 375ft-lbs Est horsepower : 390hp
Challenge: to provide a reliable, serviceable powerplant for the studio truck that will keep the gearing, provide an overdrive to increase fuel efficiency. Increase power and efficiency in the engine and maintain the PTO on the transmission to drive a hydraulic pump for a dumping bed & future hydraulics and allow for a belt driven generator.
Solution . . . A Chevy 350ci engine originating in a mid 70's musclecar with mildly ported heads to increase power and efficiency and an NV4500, 5 speed transmission. The transmission originates from a 1993 Chevrolet 3500 and is capable of handling 450ft-lbs of torque. A Chelsea pto was added to the passenger side to drive a hydraulic pump and/or generator and the 5th gear is a 0.73 overdrive.
|
|
|
|
|
|
|
|
|
|
|
|
|
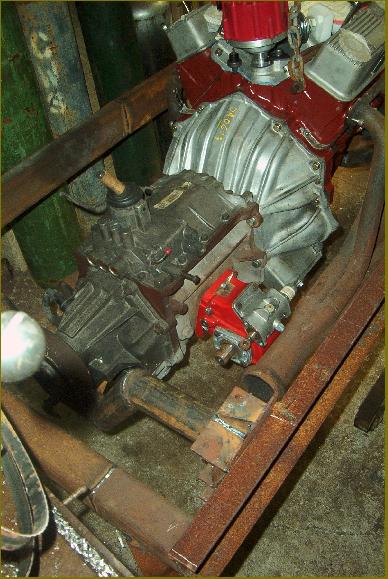 |
|
|
|
|
|
|
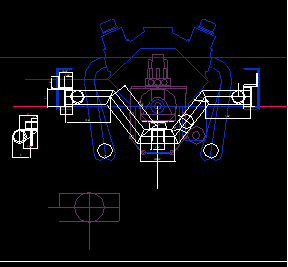 |
|
|
|
|
|
|
|
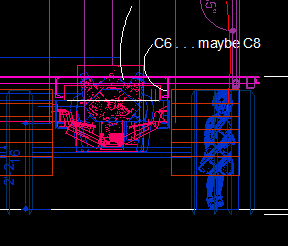 |
|
|
|
|
|
|
|
|
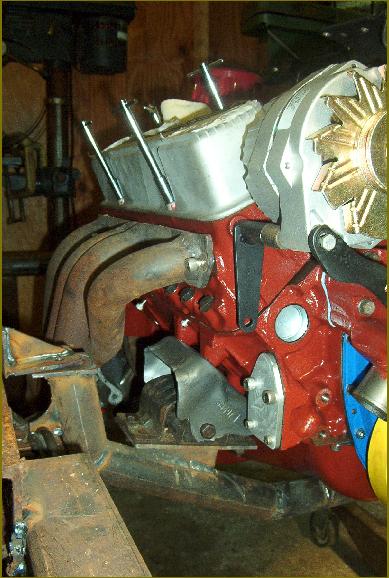 |
|
|
|
|
|
|
|
|
|
|
Above shows the NV4500 with its pto . . . One issue is the header interference. The header angle must be modified by cutting at the manifold flange and re-welding to clear the pto. The new transmission cross-member is seen here, made of 2" pipe.
Above,right: a front engine mount cross-member had to be designed and fabricated and mounting plates welded to accept stock chevy motor mounts. In the foreground can be seen the hand-made fuel pump block off plate--made of 1/4" 6061 T-6 aluminum plate.
Right: design drawings for the new cross-members.
|
|
|
|
|
|
|
|
|
|
|
|
|
|
|
|
Here is the engine/transmission on its temporary mounting frame, the caster-wheeled frame is made to the dimensions of the truck frame in order to resolve interference issues with engine components and the International frame.
|
|
|
|
|
|
|
|
|
|
|
|
|
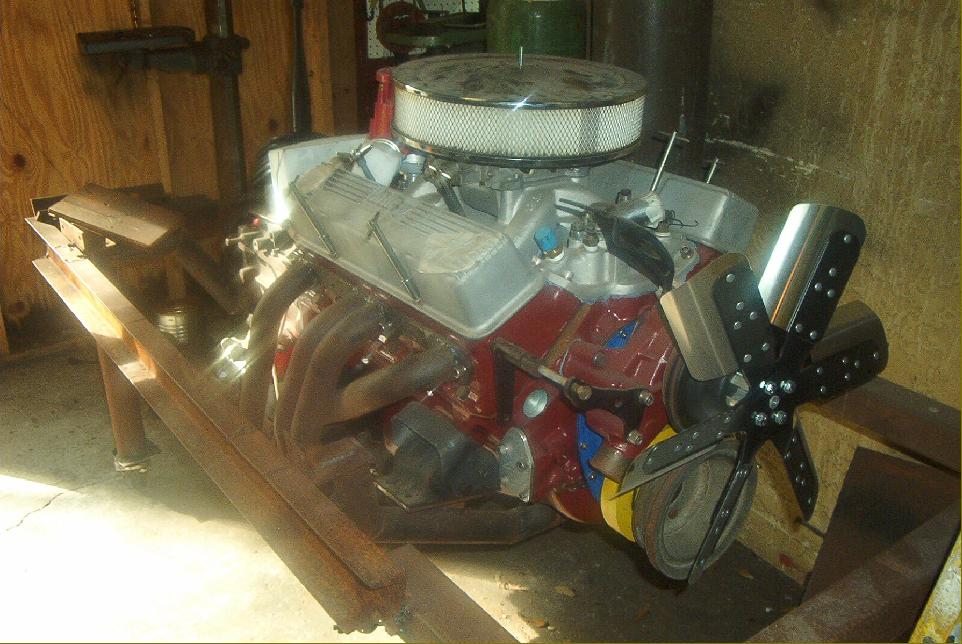 |
|
|
|
|
|
|
|
|
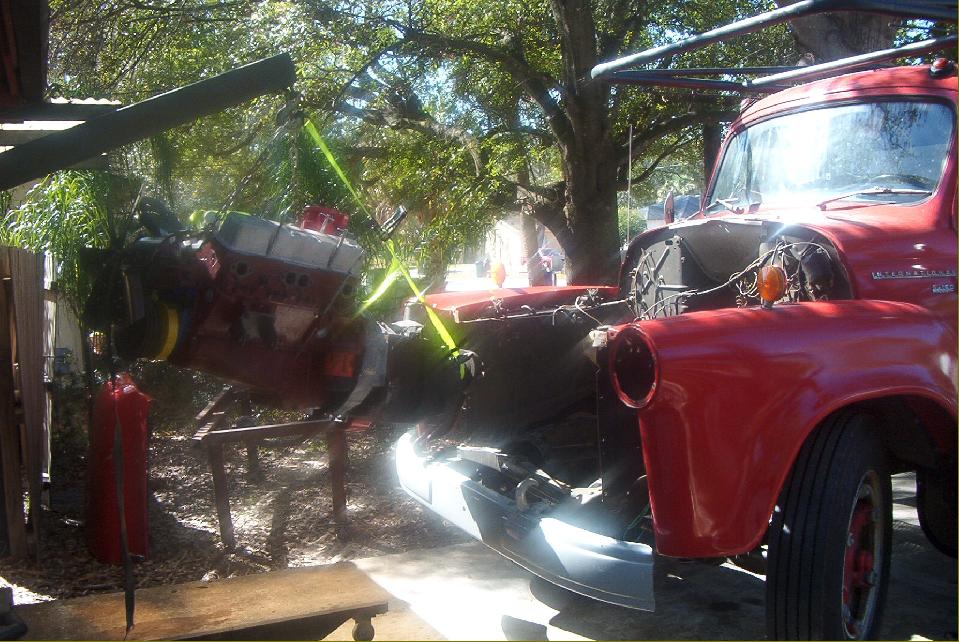 |
|
|
|
|
|
|
|
Out with the old, in with the new.
|
|
|
|
|
|
|
|
|
|
|
|
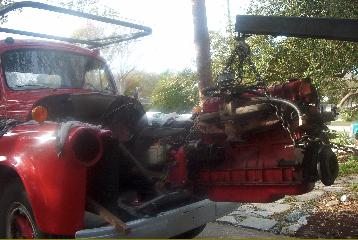 |
|
|
|
|
|
|
|
|
|
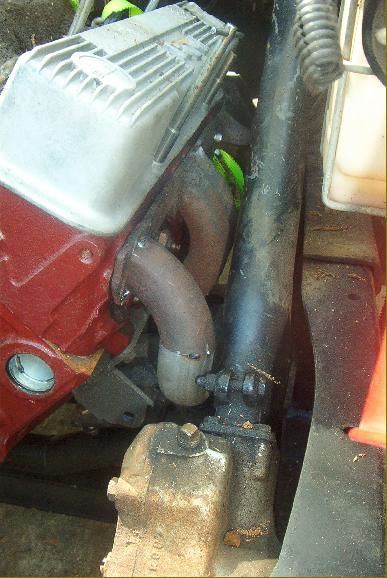 |
|
|
|
|
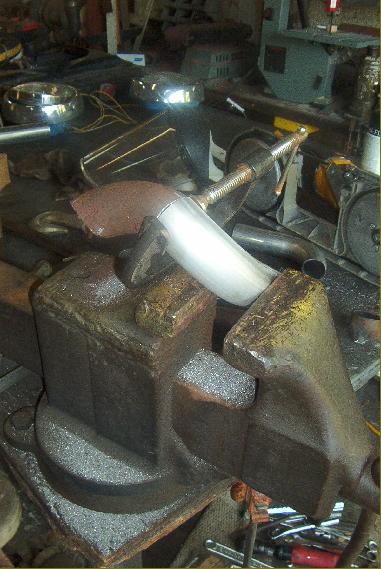 |
|
|
|
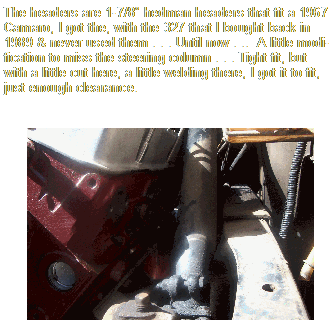 |
|
|
|
|
|
|
|
|
|
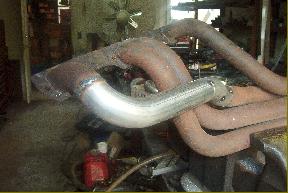 |
|
|
|
|
|
|
|
|
|
|
|
|
|
|
|
|
|
|
Here it is, all stuffed in & working . . . Here's one for Paul Luevano--Thanks for the Edelbrock--works great, nice smooth power, inexpensive rebuild kit.
|
|
|
|
|
|
|
|
|
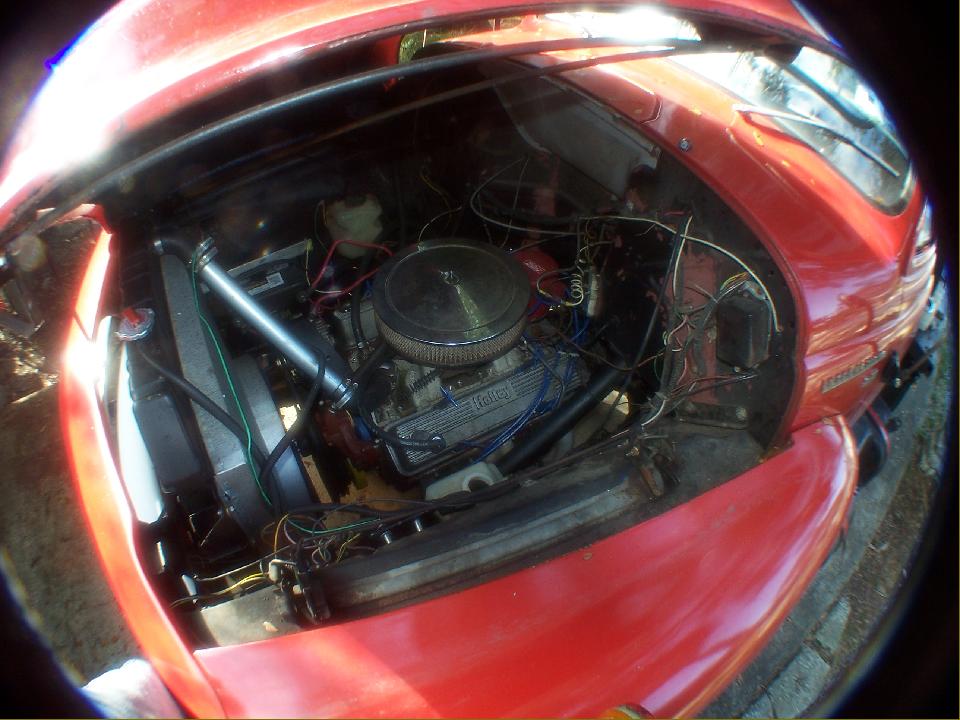 |
|
|
|
|
|
|
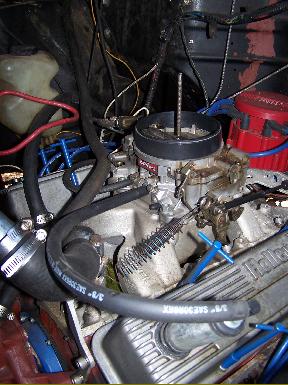 |
|
|
|
|
|
|
|
|
|
|
|
|
|
Another fabrication job I had to do was to build a fan shroud from scratch, some 26 gauge galvalume sheetmetal, my trusty, 40" metal brake & here I have it. Also, notice the fan is an anodized blue aluminum unit here & a black & stainless one in previous photos. The frame cross member that I had to trim with a torch was too close to the flex fan & the fan pulled itself into it a couple of times & destroyed itself. I got a shorder fan spacer & went to this stiffer unit & solved the issue. The radiator is also an adapted unit, he radiator is a 3 core from an unknown donor veh. & the rad. Support is the original that I modified by cutting about 3 inches out of the width to accommodate the new, updated radiator.
|
|
|
|
|
|
|
|
|
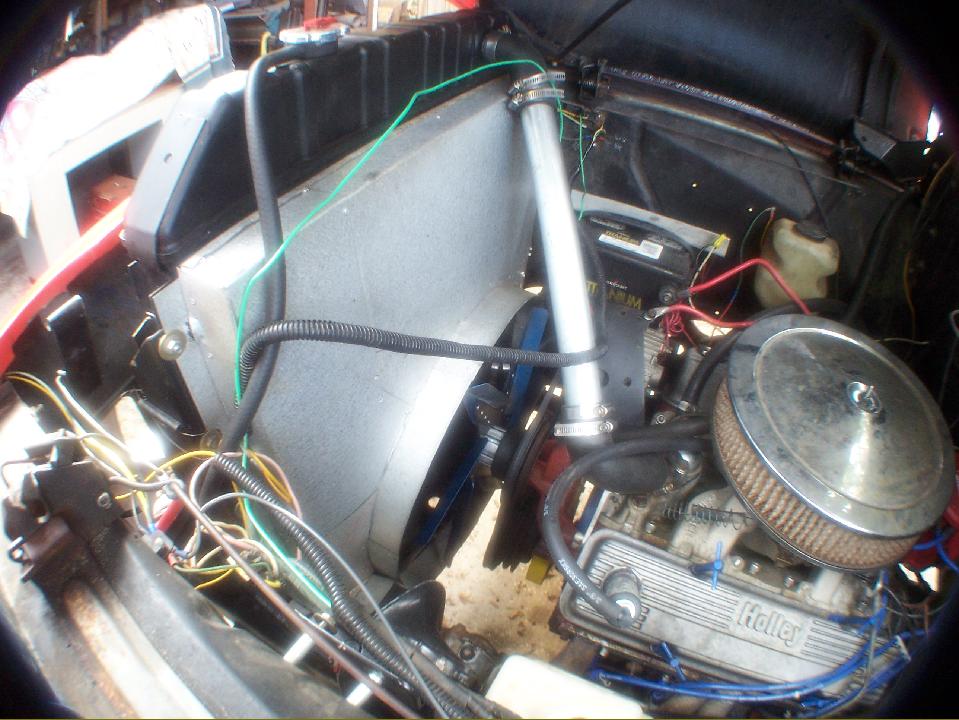 |
|
|
|
|
|
|
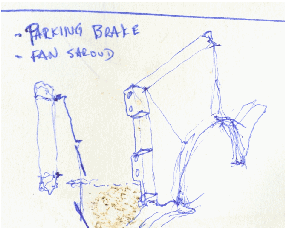 |
|
|
|
|
|
|
|
|
|
|
|
|
|
Here are drawings/sketches of the parking brake hub that I had to machine from a solid 7" dia. Steel bar & have welded into the driveshaft.
Lower left there are initial sketches of the mounting bracket . . . See the next page for more photos
|
|
|
|
|
|
|
|
|
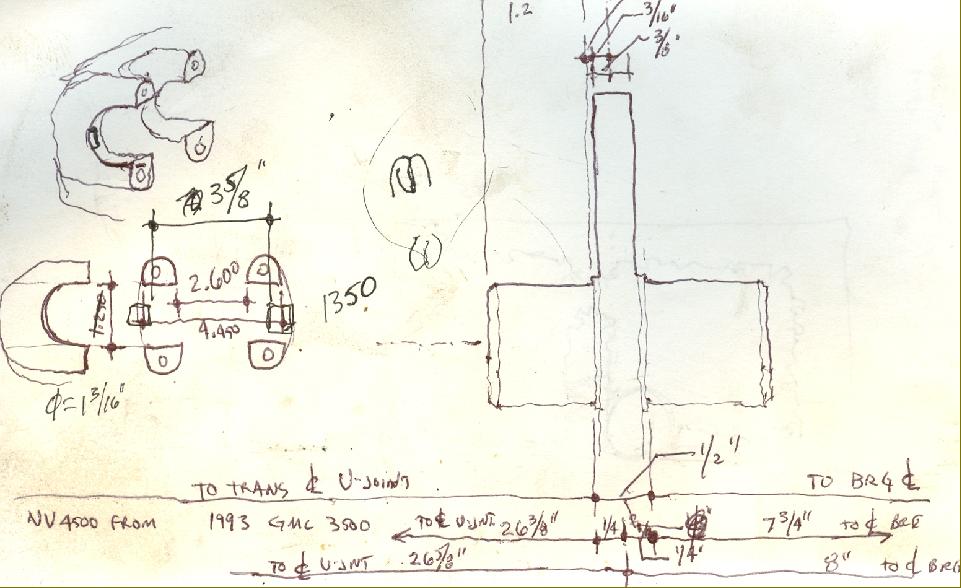 |
|
|
|
|
|
|
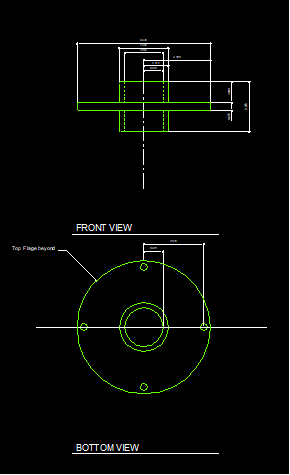 |
|
|
|
|
|
|
|
|
|
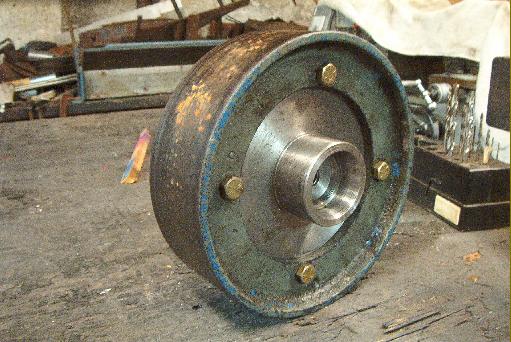 |
|
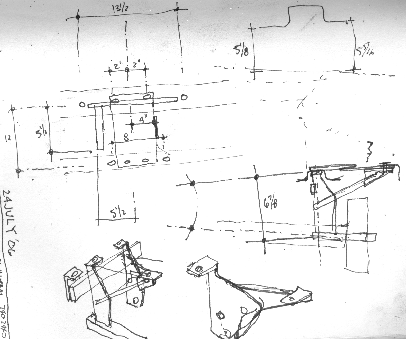 |
|
|
|
|
|
|
|
|
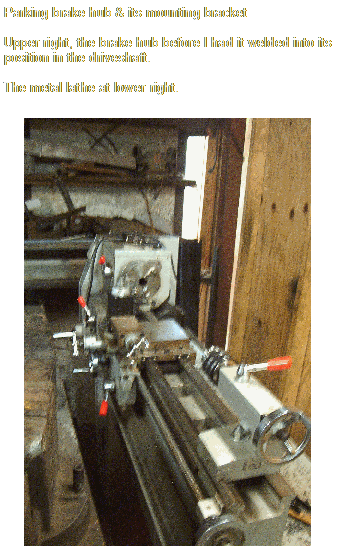 |
|
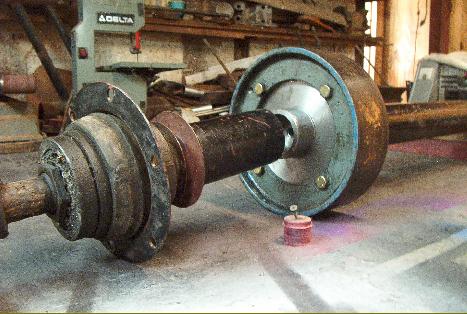 |
|
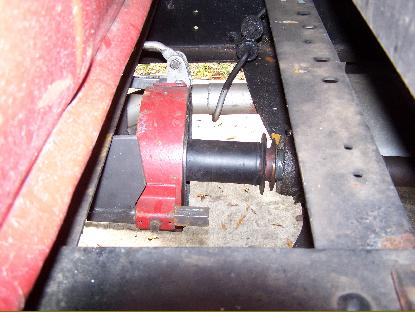 |
|
|
|
|
|
|
|
|
|
|
|
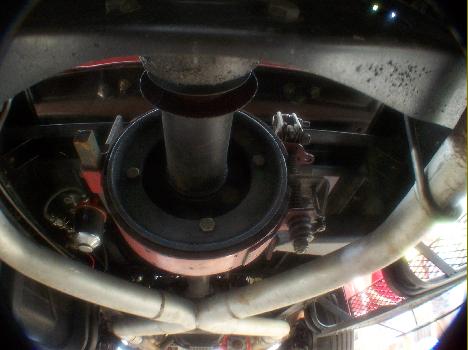 |
|
|
|
|
|
|
|
|
|
|
|
|
These are some fun parts made with aluminum flat bar & angle, fuel pump block off plate, accelerator cable stay, & accelerator spring hook.
|
|
|
|
|
|
|
|
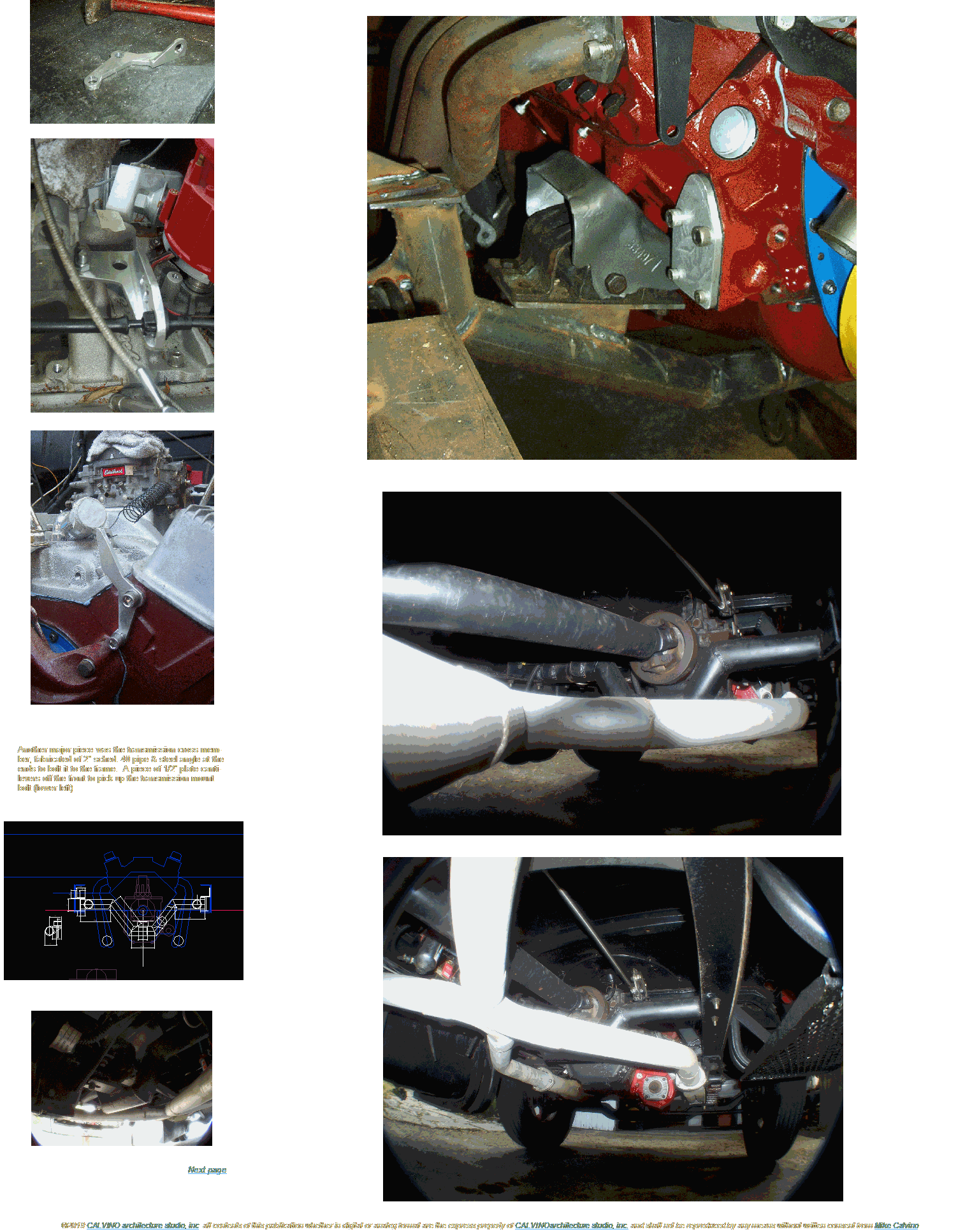 |